Runner system, flowing part of plastic injection
Runner System Construction
Sprue
sprue will contact first time with melt plastic, at the injection process, sprue always contact with nozzle from the injection machine, so consider when design the sprue consider the ball radius of nozzle, make sure it isn't make undercut on sprue.The dimensions of the sprue depend primarily on the dimensions of the molded part in particular the wall thickness, too little sprue will make sprue cold faster and make insufficient flow.
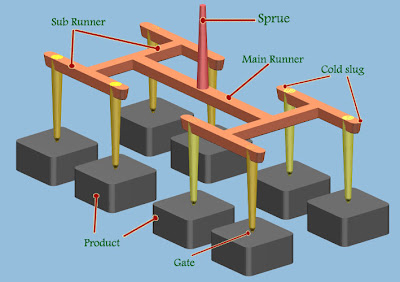
Main Runner
First time when design runner system, determine number of cavities, shape and gate types, then arrange the cavity layout,at the multi cavity of mold balancing of runner is important, balancing ensures virtually equal flow of plastic trough each gate.
To achieve balancing runner layout must be though,
Sub Runner
this part will continues flow from main runner until the gate, the dimension of sub runner and how much sub runner system will be, is very depending on how much cavity of the mold, and how the layout, what the layout use herring bone, H type, or star type. at the picture above use H type runner layout.
Cold Slug
when runner layout bent, clod slug may be required to continue plastic flow of better quality to the cavities.The cold slug well helps the flow of material through the runner system by stopping colder, higher viscosity material moving at the forefront of the molten mass entering into the cavity.The length of the well is usually equal to or greater about 1,5-2 time than the runner diameter.
Gate
Basic purpose of the gate is to limit the flow of the melted plastic, but it must allow that melted plastic flow and fill the cavity easily.
considering the fluidity of the material, gate should be made near the center of gravity of molding or the line to make flow uniform and melted material even, then make the gate thick but still considering melted plastic material, becouse thin part will cooled easily and faster.
the gate type is very various depend on part shape, mold layout, mold system, etc, here some explanation about design those gate type:
1. Direct gate
2. Side, edge gate
3. Tab gate
4. film gate
5. fan gate
6. Disc gate
Runner geometry
they are various geometry that we can use in runner, such us
1. full round
2. half round
3. trapezoid
use full round and trapezoid shape is recommended in various mold. Half round runners are not recommended because of their low volume to surface ratio
here some area calculation of cross section of runner (source : http://www.dsm.com)

Runner dimensions
The diameter of a runner depends on its length in addition to the part volume, part flow length, injection machine capacity, and gate size, Generally runner must never be smaller than the largest wall thickness of the product, it's usually make from 3 mm until 15 mm. picture below shown relation between runner diameter and maximum runner length (source : http://www.dsm.com)

The runner should be large enough to minimize pressure loss, yet small enough to maintain satisfactory cycle time, Large runners are not economical because of the amount of energy that goes into forming, and then regrinding the material that solidifies within them.
Runner layout
In general they are three type of runner layout
1. "H" bridge (branching) runner system
2. Standard (herringbone) runner system (conventional runner)
3. Radial (star) runner system
look at picture below shown standard runner and H bridge type runner.

and below is star layout runner system (both bottom picture)

Balancing the runner system ensures that all mold cavities fill at the same rate and pressure, if the product have not similar product geometry, it is recommended to use mold analysis software like mold flow or C-Mold.